Ball milling is a process that is commonly used in the mining industry for the purpose of crushing and grinding ores into finer particles. The process involves feeding the material into a rotating drum, which contains steel balls that break up the material and grind it down into a finer powder. This process is essential in many industries as it allows for the extraction of valuable minerals and metals from ore. In this blog, we will be looking at the various factors that affect the efficiency of ball milling.
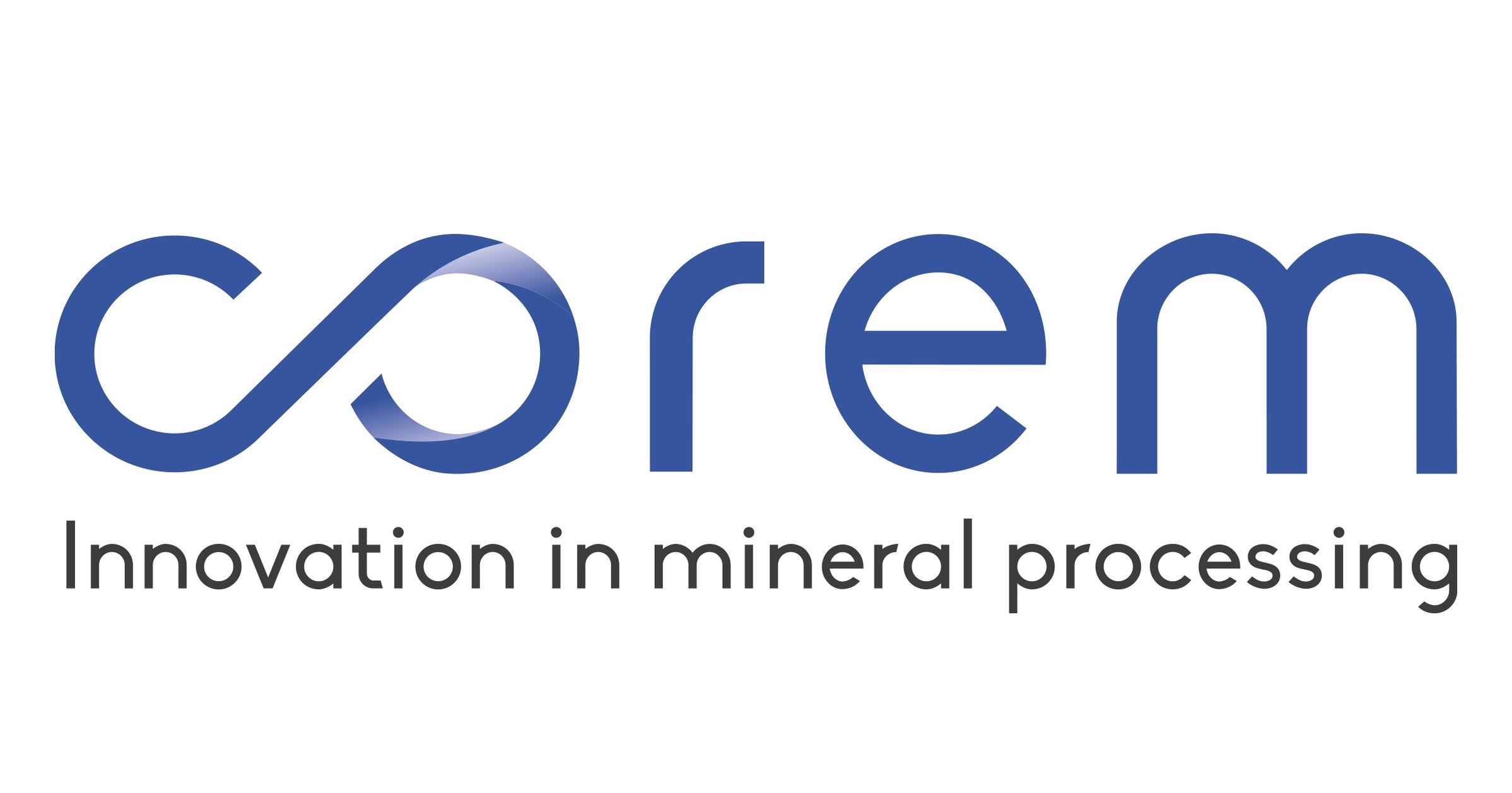
Crushing Action of Ball Mills
The crushing action of ball mills is achieved by the balls dropping onto the material to be crushed. The balls are usually made of steel and vary in size, depending on the application. The size and weight of the balls also affect the efficiency of the process. Smaller balls may not break the material down as effectively as larger ones, while heavier balls may generate excessive wear and tear on the mill liners.
Conditions Determining Fineness of Crushing
The fineness of the crushed material is determined by a number of factors, including the size of the balls, the speed of the mill, and the time the material spends in the mill. The finer the material needs to be crushed, the smaller the balls and the slower the mill needs to operate. This is because smaller balls can deliver more crushing action per unit of time, and slower speeds allow the material to spend more time in the mill.
What Affects Ball Mill Capacity
Ball mill capacity is affected by several factors, including the hardness of the ore, the feed size, and the product size. Harder ores require more crushing power and a larger ball size. Larger feed sizes require larger ball sizes, while smaller product sizes require smaller ball sizes. The capacity of the mill is also affected by the percentage of solids in the milling circuit. Higher solids concentrations lead to lower capacities, as there is less room for the ore and balls to move around in the mill.
Conditions Affecting Ball Mill Power
The power requirements of the ball mill are affected by a number of factors, including the speed of the mill, the size and weight of the balls, and the amount of charge in the mill. Higher speeds require more power as the balls generate more kinetic energy, while larger balls and higher charges require more power to overcome the increased friction and resistance in the mill.
Ball Mill Crushing
Ball mill crushing is a process that involves the material being crushed between the balls and the mill liners. The balls and liners are both subject to wear and tear during the crushing process, which can lead to reduced efficiency and increased maintenance costs. To minimize wear and tear and maximize efficiency, it is important to choose the right type of grinding steel ball and mill liner for the application.
How to Feed a Ball Mill
Feeding a ball mill involves introducing the material into the mill at a controlled rate. The rate of feed will depend on the size and hardness of the material, as well as the required fineness of the crushed product. It is important to ensure that the mill is not overfed, as this can lead to blockages and reduced efficiency.
Consistency of Pulp in Ball Mill
The consistency of the pulp in a ball mill is important for maintaining efficient operation. Inconsistent pulp densities can lead to reduced grinding efficiency and increased power consumption. To maintain consistent pulp densities, it is important to monitor the mill feed and adjust the water or chemical additives as needed.
Grinding Ball Consumption
Grinding steel ball consumption is a major factor in ball mill efficiency. The cost of replacing worn balls can be significant, so it is important to choose the right type of grinding ball for the application. Higher hardness balls are more resistant to wear and last longer, but are more expensive upfront. Lower hardness balls are cheaper, but will wear out more quickly and require more frequent replacement.
Ball Mill Liner Consumption
Mill liner consumption is also an important factor in ball mill efficiency. The wear and tear of the mill liners can lead to increased energy consumption and reduced capacity. To minimize liner wear, it is important to choose the right type of liner for the application, and to maintain the liners through regular inspection and maintenance.
In conclusion, ball milling is an essential process in many industries, and its efficiency is affected by a number of factors, including the size and weight of the balls, the feed size and product size, and the type of grinding steel ball and mill liner used. By choosing the right equipment and maintaining it properly through regular inspection and maintenance, the efficiency of the ball milling process can be maximized, leading to increased profitability for the business.