Introduction:
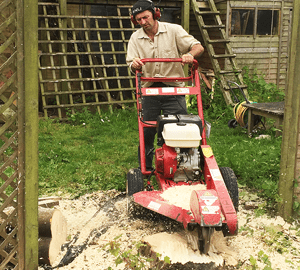
In the world of cement manufacturing, grinding plays a crucial role in achieving the desired fineness of the final product. Grinding cylpebs have emerged as a revolutionary solution, offering unique advantages over traditional grinding media. With their stable quality, high production efficiency, and wear-resistant properties, grinding cylpebs have become the go-to choice for cement manufacturers worldwide.
Grinding Cylpebs: A Superior Grinding Media Solution
Grinding cylpebs, also known as slightly tapered cylindrical grinding media, are made from low-alloy chilled cast iron. This manufacturing process ensures high hardness and wear resistance, with a volumetric hardness ranging between 60-63HRC. Additionally, their compact organization and constant hardness from the inner to the surface make them ideal for cement grinding applications.
Enhanced Performance and Cost-effectiveness
Utilizing grinding cylpebs in cement production leads to numerous benefits, chief among them being the reduced wear rate. Studies have shown that grinding cylpebs exhibit a wear rate of about 30g-60g per ton of cement, making them highly durable and cost-effective.
The manufacturing process of grinding cylpebs significantly contributes to their cost effectiveness. By employing an automatic production line, the production efficiency is maximized. The low-alloy chilled cast iron is cast into shape using a continuous casting machine, resulting in cylpebs with a precise diameter and length. This efficient process reduces energy consumption compared to conventional forging methods, providing further economic benefits.
Surface Area and Bulk Density: Unlocking Greater Efficiency
The cylindrical geometry of grinding cylpebs offers distinct advantages over traditional grinding media. Due to their shape, cylpebs have a 14.5% greater surface area and a 9% higher bulk density compared to steel balls of similar mass. In fact, they even outperform cast balls, with a 12% higher bulk density.
Consequently, using cylpebs in a grinding mill enables a higher surface area for size reduction, resulting in improved grinding efficiency. However, it is important to note that this increased efficiency may lead to a higher power consumption by the mill.
Conclusion:
Grinding cylpebs have revolutionized the cement industry with their exceptional quality, high production efficiency, and wear-resistant properties. With a wear rate of only 30g-60g per ton of cement, these cylpebs offer durability and cost-effectiveness like never before.
Utilizing an automatic production line, cylpebs are manufactured with precision and consistency, resulting in superior grinding performance. Their cylindrical geometry offers a greater surface area and higher bulk density, leading to enhanced efficiency in grinding mills.
The future of cement grinding lies in adopting grinding cylpebs as the go-to grinding media. Their unique properties, cost-effectiveness, and efficiency will undoubtedly drive the industry forward, ensuring a successful and sustainable future for cement manufacturers.
Keywords: Grinding Cylpebs, cement industry, grinding media, wear rate, production efficiency, cost-effectiveness, surface area, bulk density, grinding mills.